The ultimate spray drying solution.
Spray drying is applied to any pumpable product such as emulsions, pastes, solutions and suspensions.
Labmaq do Brasil manufactures and supplies spray dryers of different scales according to the demand and needs of its customers, with its own projects and innovative designs. They are compact, versatile, robust and offer excellent results, performance and powders with high performance in spray drying. In addition, they cover a wide range of applications in the pharmaceutical, food and beverage, agriculture, chemical, polymer, ceramics, cosmetics and aroma industries, among others.
Equipment with capacity above 10L/h or with specific layout, safety, classified area requirements, etc. they are custom-made according to your needs, therefore, contact our technical-commercial sector.
MSD 3.0
Spray Dryer MSD 3.0 is a device capable of fast drying, up to 3.0L/h (water reference), of aqueous products. It features a compact and detailed module designed for use in research and development laboratory applications as well as small-scale production.
The cabinet and column are built in carbon steel with anti-corrosion treatment and electrostatic powder painting. The parts that come into contact with the materials involved in drying are all stainless steel or boron silicate glass. Its great differential is a control system and variation of the air flow with a real-time measurement system using a Pitot tube.
In addition to being robust and compact, the MSD 3.0 is easy to operate. The atomization can be monitored by the drying chamber display, made of stainless steel with internal and external polishing and sanitary finish, equipped with LED lighting. Cyclone made of polished stainless steel also has a sanitary finish. The equipment has TC series nipple type connections, facilitating the assembly, sealing and asepsis of the parts.
SAFETY
It has a dedicated panel for control and automation with PLC system, HMI touch screen for command, process reporting, graphics and USB output for data capture. It is equipped with an emergency button for greater security and protection of the system, in addition to alarms and interlocks in cases of high temperature or low flow.
The equipment comes with a complete Operation Manual and SOP suggestion (Standard Operating Procedure). We also provide a list of spare parts and access to a video tutorial with step-by-step instructions on how to assemble and operate your equipment. By becoming a Labmaq partner, you will also have exclusive access to our database of scientific articles in which you have hundreds of articles and literature published on our equipment.
MSD 3.0 | |
Capacity | Up to 3.0L/h (ref. water) |
Atomization | Double Fluid (Pneumatic) - Bottom Spray |
N° of nozzles included | 2 |
Max. Energy Consumption | 10,500W |
Voltage | 220V or 380V |
Compressed air consumption | Up to 50L/min |
Recommended compressed air pressure | 6 bar |
Maximum operating temperature | 250°C |
Maximum feed flow | 3.0L/h (ref. water) |
Dimensions in mm (LxHxW) | 1,365 x 2,315 x 780 |
Customizable Filtration System
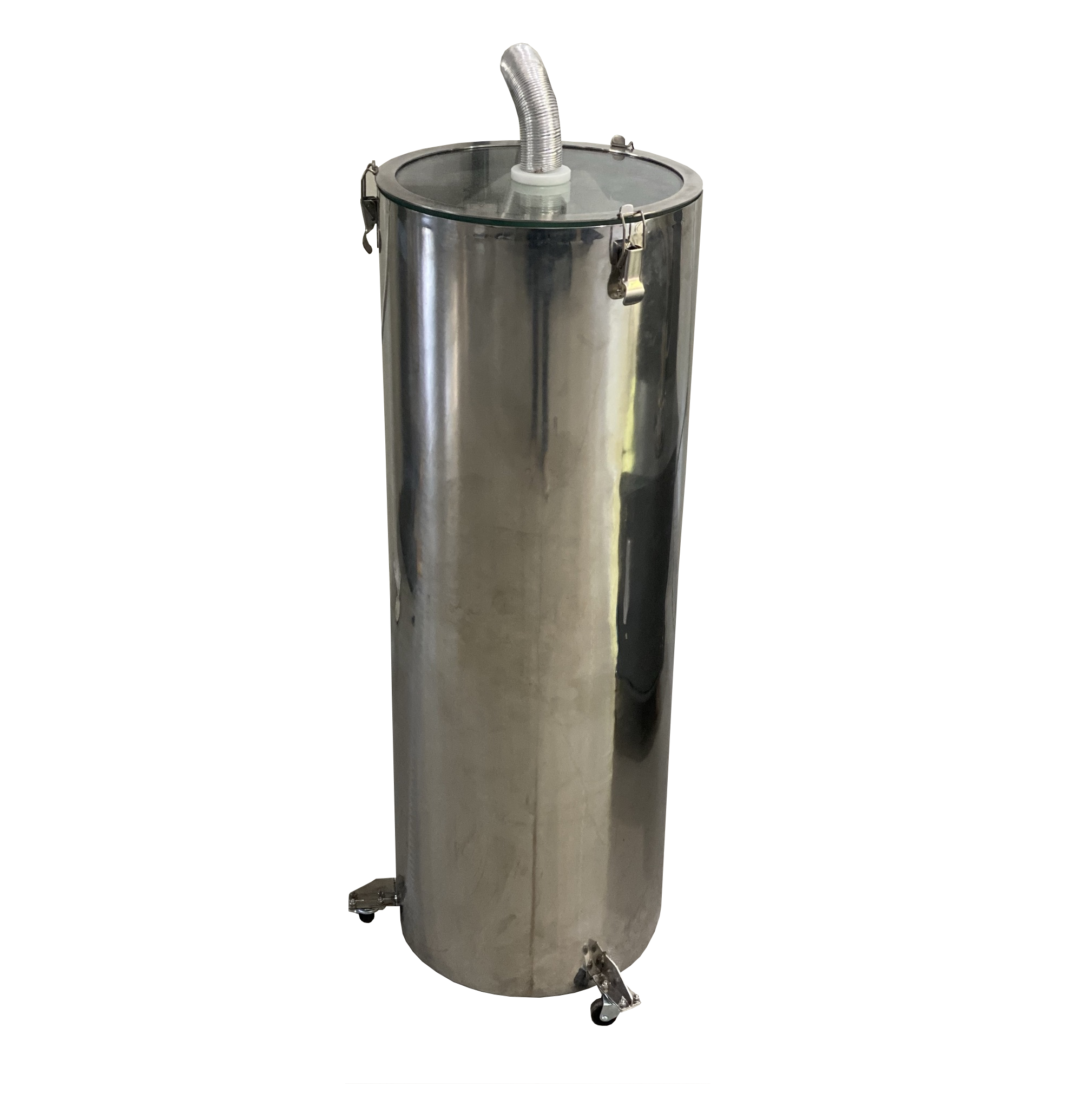
Filtration systems are bag filter systems for connection to the dust separator cyclone outlet. They are designed for different flows and materials, aiming to meet the most diverse applications.
They consist of an AISI 304 stainless steel structure with casters to facilitate movement and bag filters to retain particles of a wide range of sizes. These sleeves can be made of polypropylene, polyethylene, polyester, among others, and have openings in their fabric to retain particles from 1 micron, depending on the application.
Customizable Stainless Steel Feed Tank
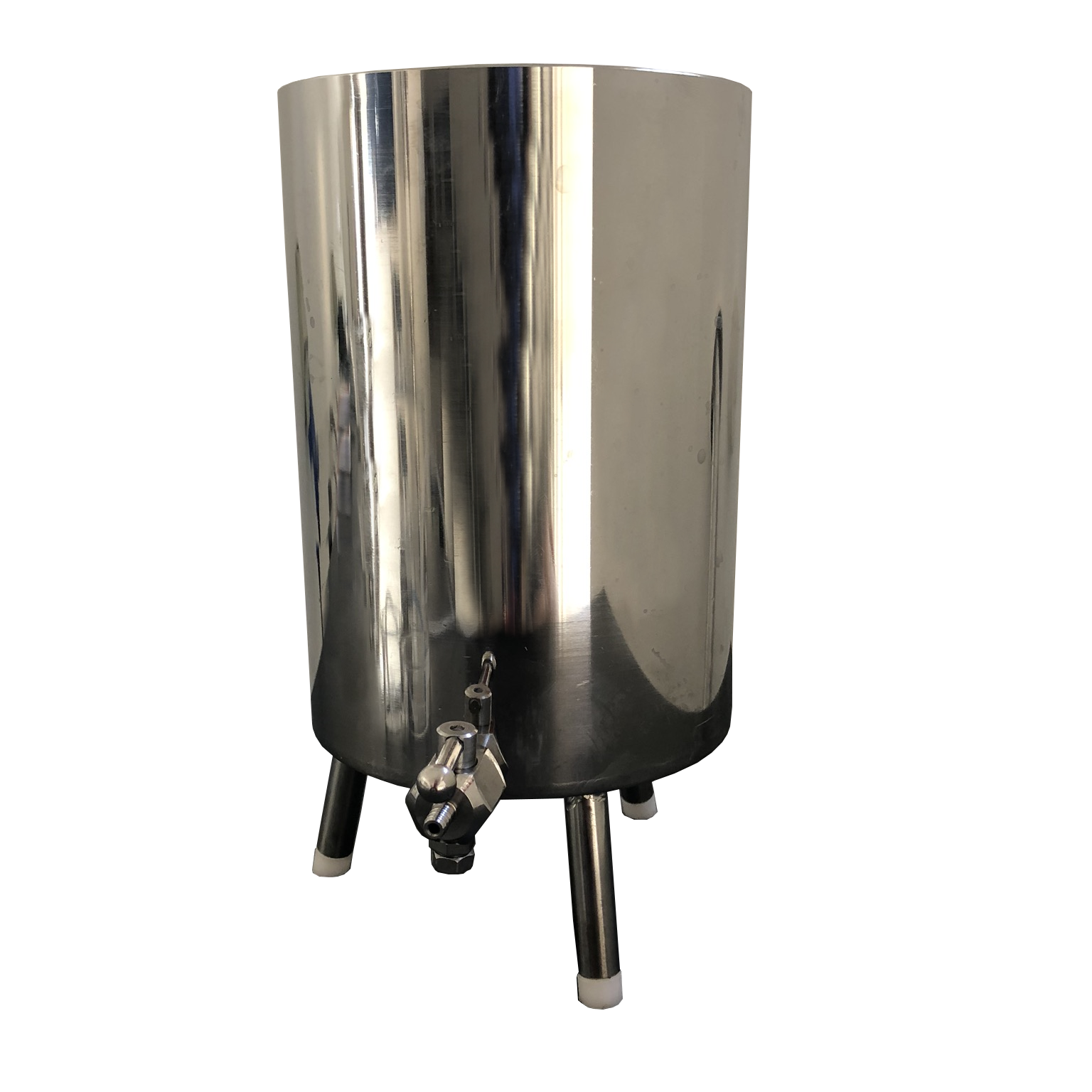
Variable volume stainless steel mini tank with a curved bottom and open/close valve for full use of samples.
Model comparison table
Operation
Spray drying techniques start with the preparation of the liquid sample, and may include several processes such as extraction, concentration, mixing, homogenization, formulation, additives, among others. It is important to highlight that the solids content is what will determine the amount of liquid that is being evaporated and the amount of powder that will result from drying. Therefore, concentrating your product before feeding it into the equipment can save you money and increase productivity.
Afterward, the product can be fed into the system, which is done from an atomization system that is formed by a nozzle or a rotary atomizer. This system transforms the liquid solution or suspension into thousands or even millions of droplets that come into contact with the heated drying gas, initiating evaporation and forming the solid product. This technique is based on increasing the contact surface to increase mass and thermal exchange efficiency. This same drying gas, which is normally ambient air, transports these particles out of the chamber to the cyclone, which separates the gas with the evaporated moisture from the powder particles. Thus, dust is collected in the lower part of the cyclone and in the upper part there is the air/gas exit from the process.
Thus, this process includes two large groups of variables for optimization and development: the formulation group and the drying process group. The first refers to formulation variations such as pre-preparation, composition (such as sugar, fat and protein levels), solids content, viscosity, stability, temperature sensitivity and additives. Additives can have different objectives, such as microencapsulation, which can provide the final powder product with numerous advantages, such as wall protection against oxidation and light, masking of undesirable flavors and controlled release of the active ingredients of interest.The second refers to the process variables. Among them are the type and size of the atomization system, flow and drying gas/air inlet, product feed flow and temperature of the drying gas. They all influence the appearance and final result of the powdered product.
Advantages
The spray drying method offers some advantages over other drying methods, including:
1 - High Productivity, when compared to costs of other similar drying methods.
2 – A wide range of applications, which can be applied to practically every type of product, unlike other drying methods that can be more restricted.
3 - Easy process scalability, with availability of equipment on laboratory, pilot and industrial scales.
4 - High quality and durable powder product, as through R&D parameters and formulations can be fine-tuned, enhancing the qualities of the in natura product and increasing the shelf life of the products.
Microencapsulation by Spray Drying
Microencapsulation is the inclusion of an active substance in a solid polymer matrix forming a microsphere. It has applications in products such as essential oils, herbicides, insecticides, parasiticides, biological traps, bio pesticides, drugs, food products, mineral supplements, aromas, fragrances, and natural additives, among others.
Microencapsulation can be performed concomitantly with spray drying and preserves the active substance from the degrading conditions, prevents nutritional losses, inhibits reactions with other agents, masks color, odor and flavor, increases shelf life, reduces the risk of toxicity in the product handling and avoids contamination.
There are thousands of different additives and the first step is to assess the purity and application requirements of the final product. There are additives for the agricultural, food, pharmaceutical, cosmetic sectors. Depending on your final product, additives need to be restricted to the correct sector. The second step is to define the scope of microencapsulation and which characteristic you want the wall material to add to your final product?
Our R&D team has decades of experience with microencapsulation and we can help you develop your product. In addition, Labmaq spray dryers have all the necessary tools for microencapsulation and nebulization drying, designed in detail to be used in research in development laboratories, as well as in production and manufacturing.